MGTSTUMPY
Active Member
I loved the OEM pressing on the firewall so I welded up all the unnecessary holes for that clean look. Still a work in progress.
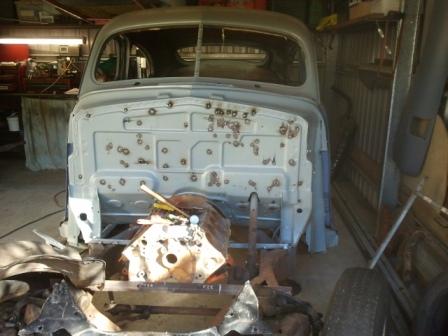
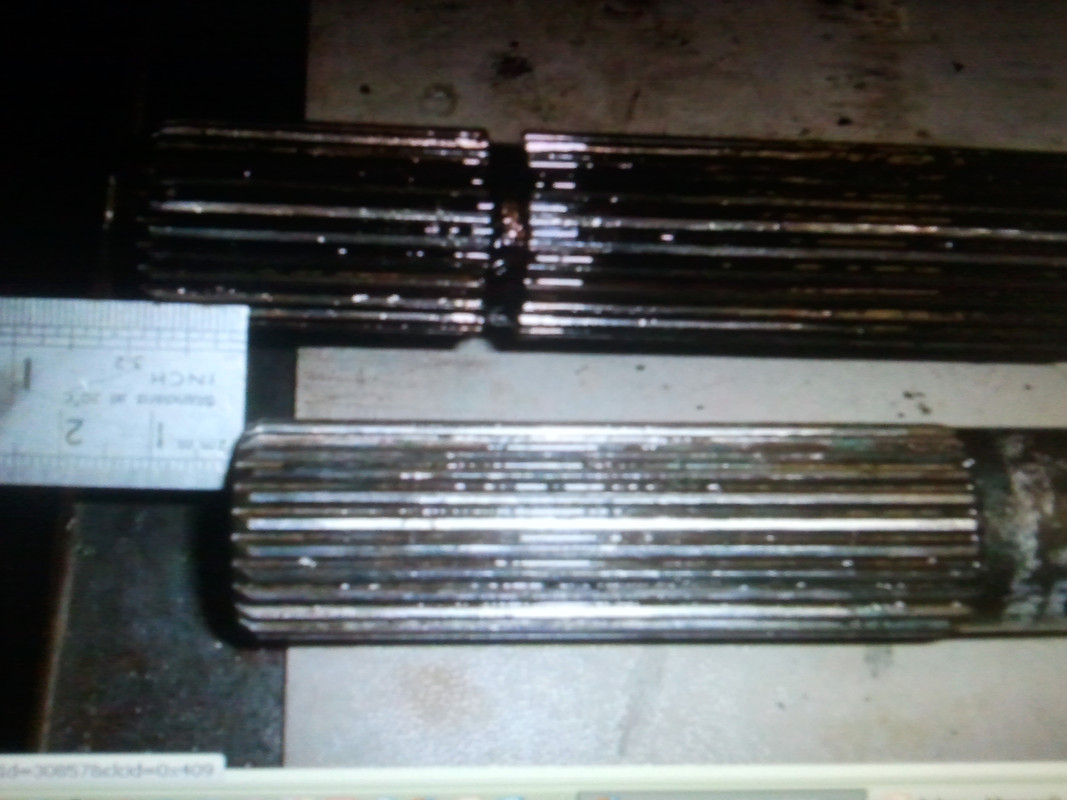
I linished the block and transmission case before painting. As the 700R came from a C4 Corvette I had to swap the extension housing and output shaft as I eliminated the OEM 'C' beam that bolted to IRS. Plus the Corvette case has no casting provision for transmission mounting. It was rebuilt and beefed up with extra internal goodies and shift kit
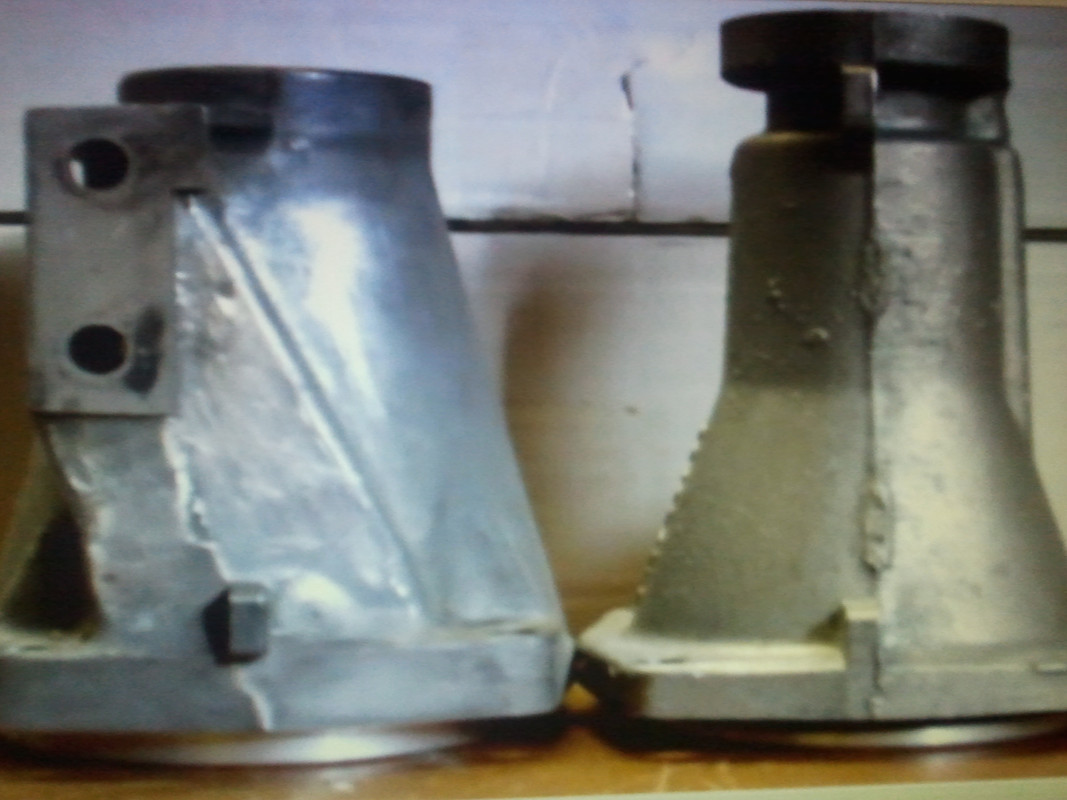

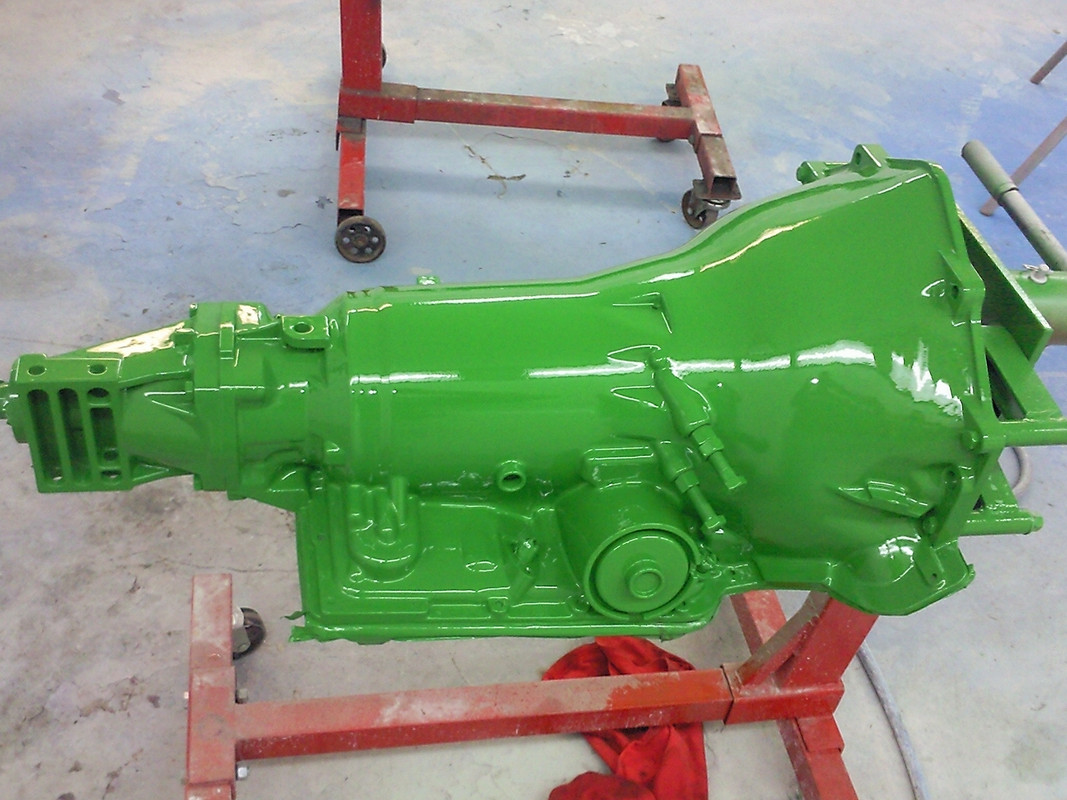
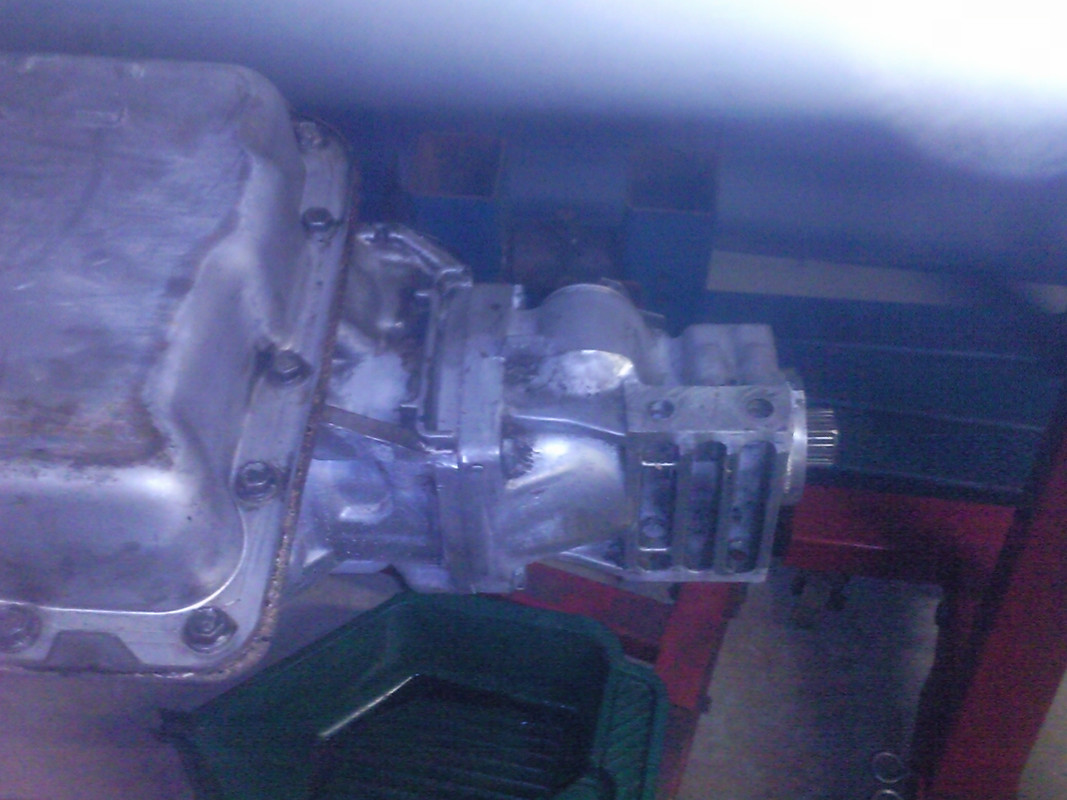
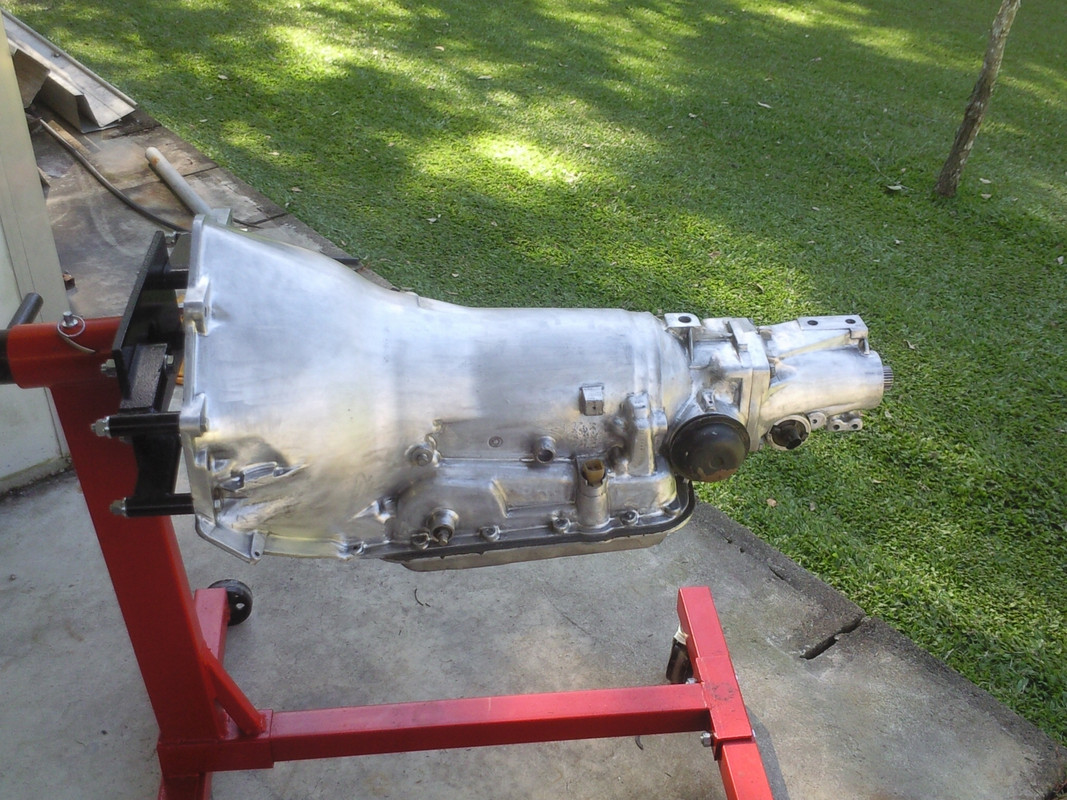
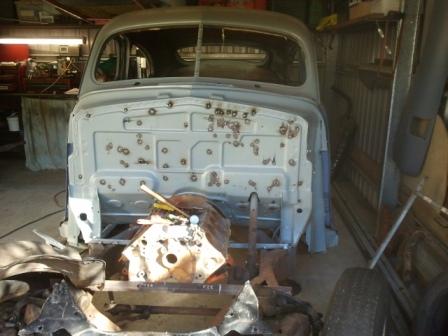
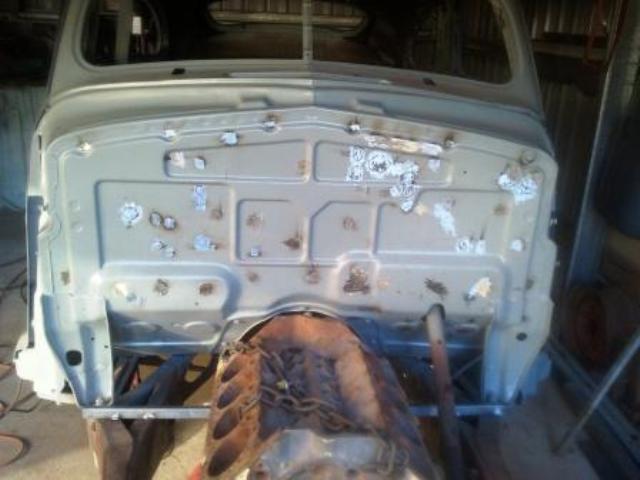
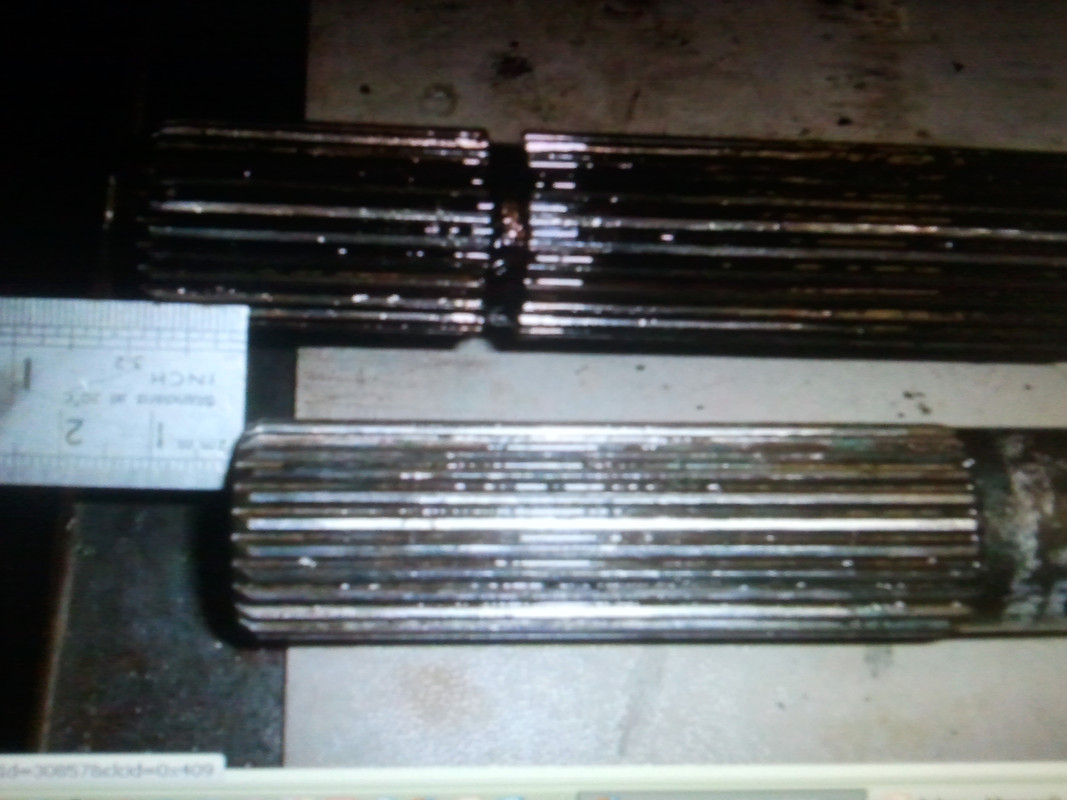
I linished the block and transmission case before painting. As the 700R came from a C4 Corvette I had to swap the extension housing and output shaft as I eliminated the OEM 'C' beam that bolted to IRS. Plus the Corvette case has no casting provision for transmission mounting. It was rebuilt and beefed up with extra internal goodies and shift kit
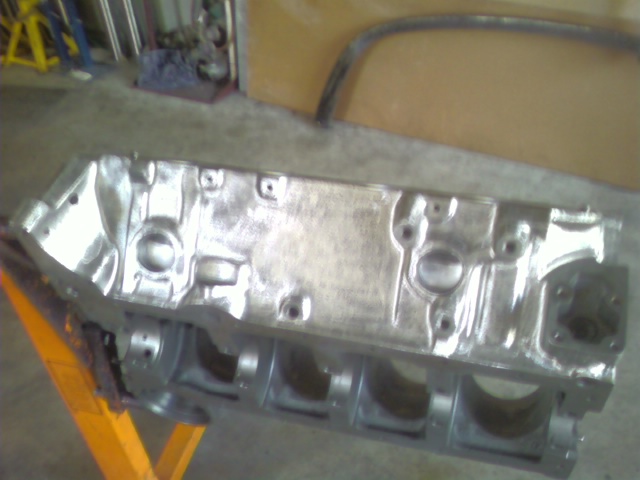
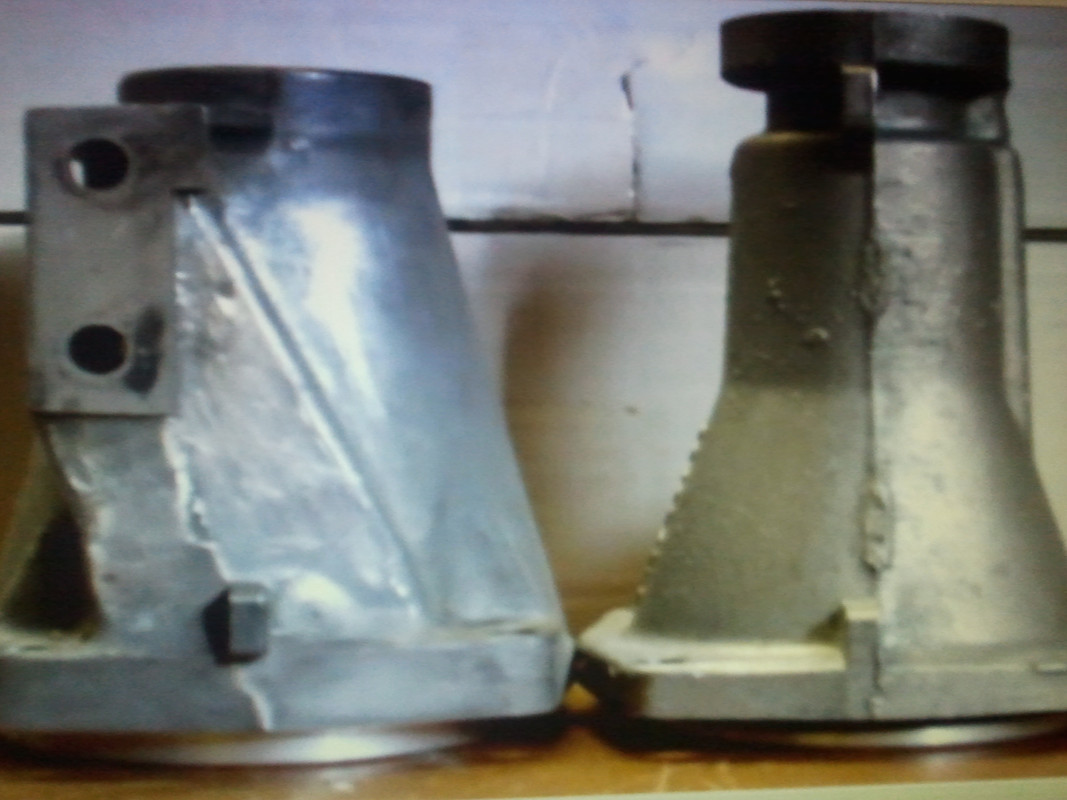

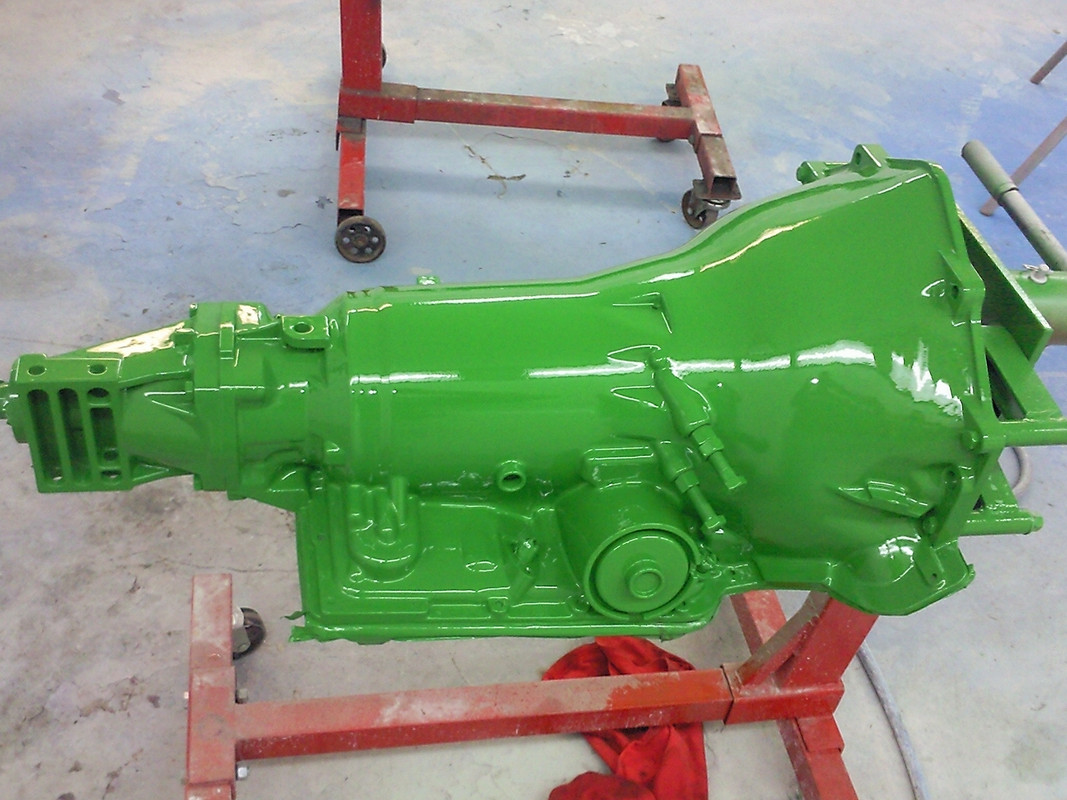
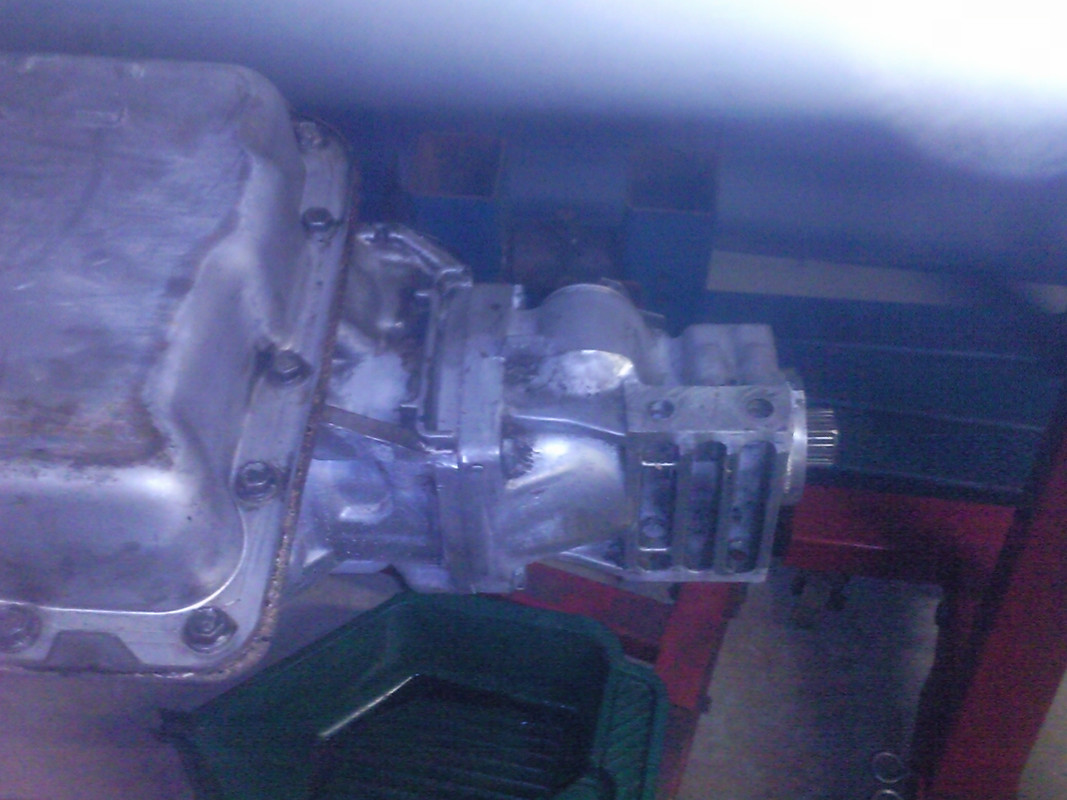
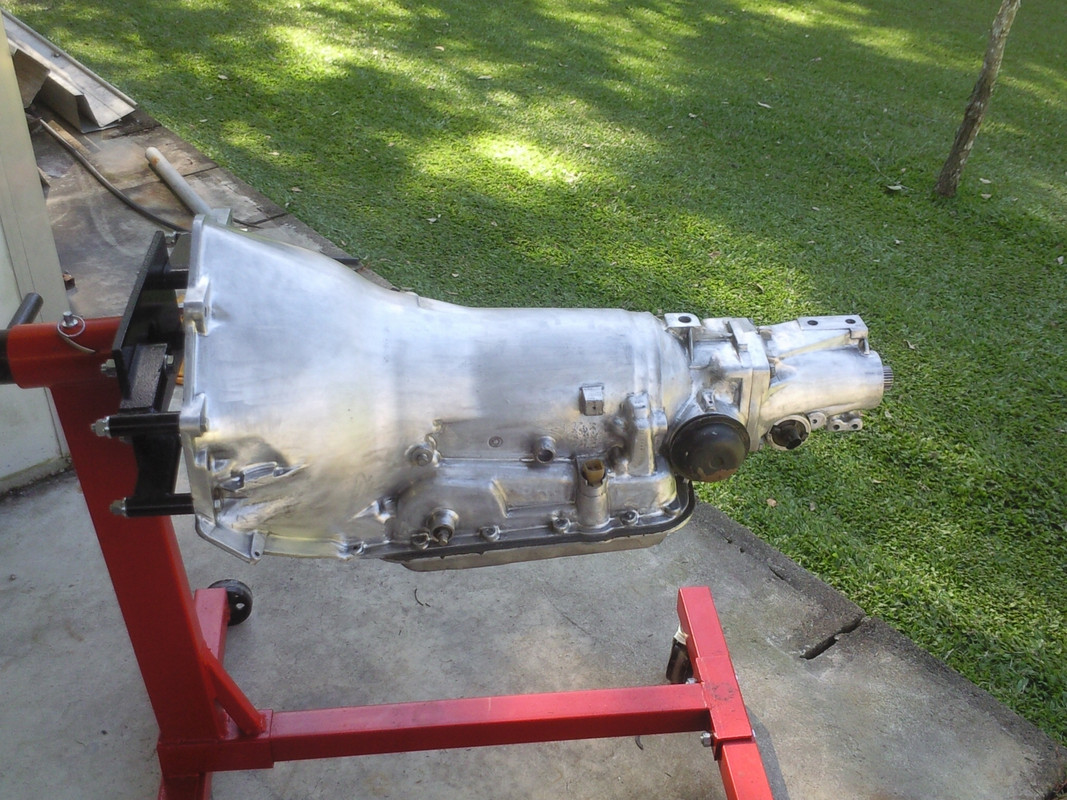