Bgbkwndow reminded me that I haven't posted about the Banjo wheel I made. I did a tech piece on another board and totally forgot to put it on here(my bad)
I said I would do a tech piece on how I made that 4 spoke banjo wheel. I made a three spoke this time but the method is the same. You could use the same technique if you wanted to "regrip" an old wheel that is all cracked or has no grip left.
First I started with a piece of MDF 2' X 4' and marked a line to split it in half.....
Next I cut the pieces and stacked them on top of each other and marked a center point and four bolt down holes and one register hole (to make sure the halves go back to the same place.)
Then I marked the two halves with arrows so I really get them oriented properly.
Next drill out the holes...!/4 for the center hole and 3/8 for the others
The next step I did was use a holesaw to make the center bigger so I can put the halves on my rotary table on my milling machine but if you only had a router you could use a circle attachment to do the same job.
Because I want the grip to be 1 inch I bought a 1 inch round router bit and chucked it in my mill
I set the bit 7-1/2 inches from the center of the rotary table and that gives me 16 inches to the outside diameter on the wheel
I set the depth at 1/2 inch and started turning the table
I said I would do a tech piece on how I made that 4 spoke banjo wheel. I made a three spoke this time but the method is the same. You could use the same technique if you wanted to "regrip" an old wheel that is all cracked or has no grip left.
First I started with a piece of MDF 2' X 4' and marked a line to split it in half.....
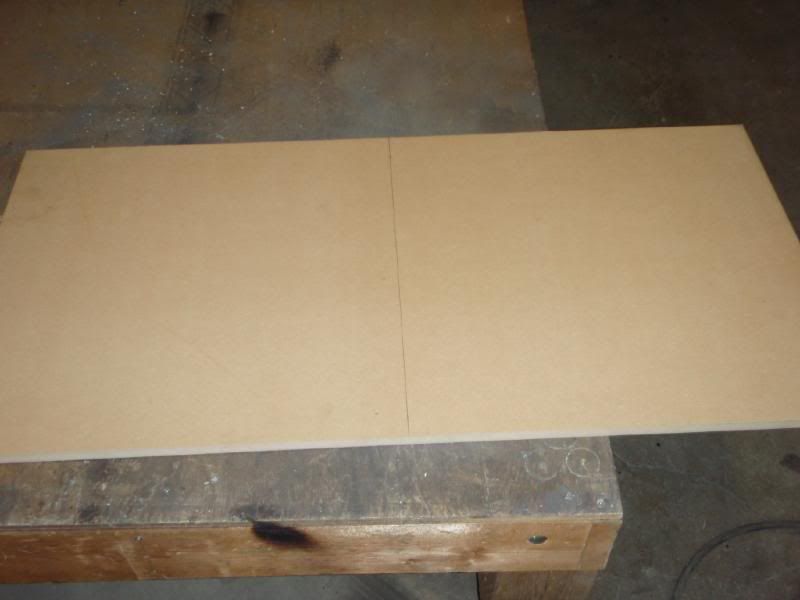
Next I cut the pieces and stacked them on top of each other and marked a center point and four bolt down holes and one register hole (to make sure the halves go back to the same place.)
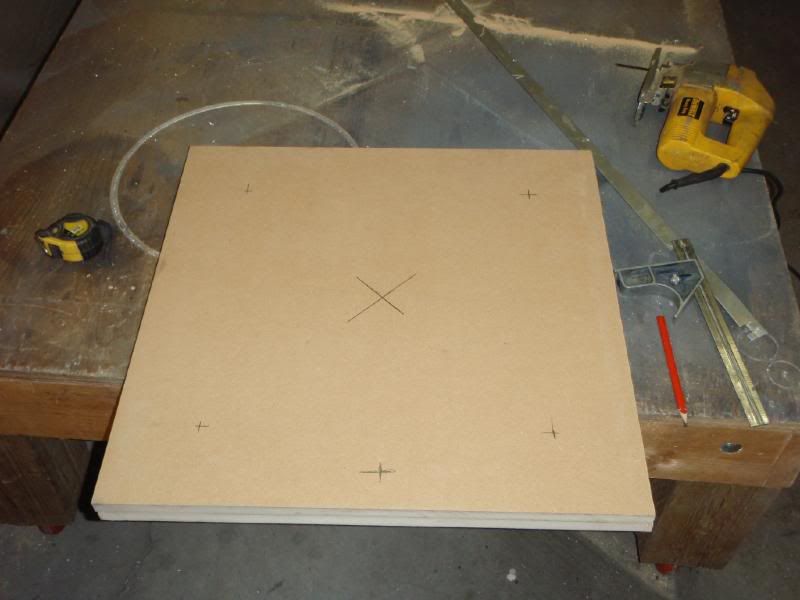
Then I marked the two halves with arrows so I really get them oriented properly.
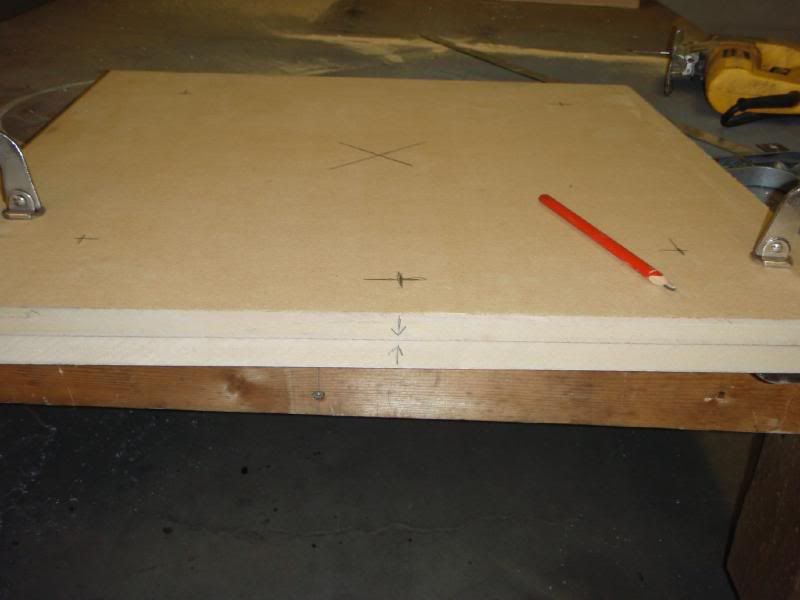
Next drill out the holes...!/4 for the center hole and 3/8 for the others
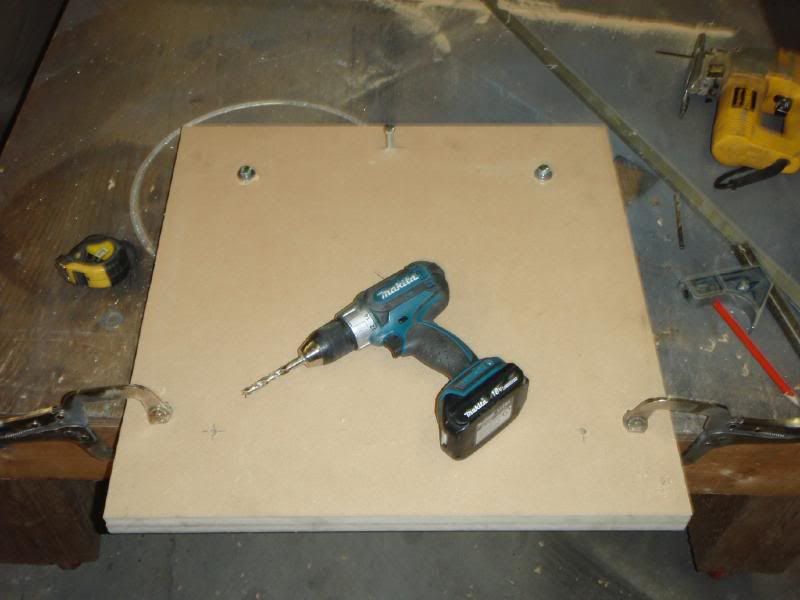
The next step I did was use a holesaw to make the center bigger so I can put the halves on my rotary table on my milling machine but if you only had a router you could use a circle attachment to do the same job.
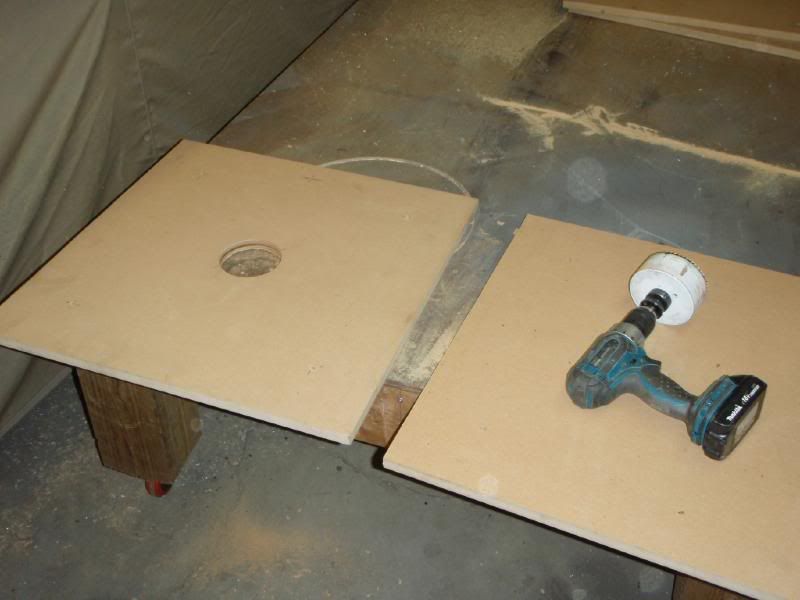
Because I want the grip to be 1 inch I bought a 1 inch round router bit and chucked it in my mill
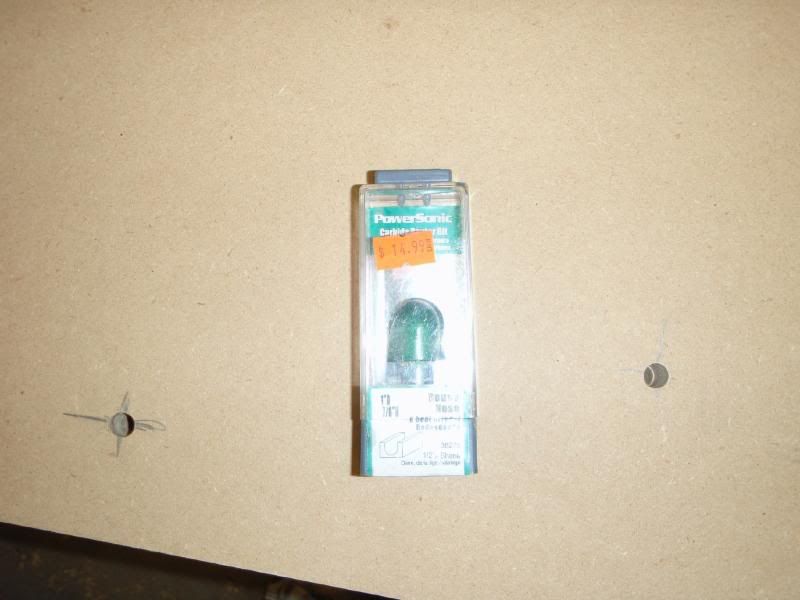
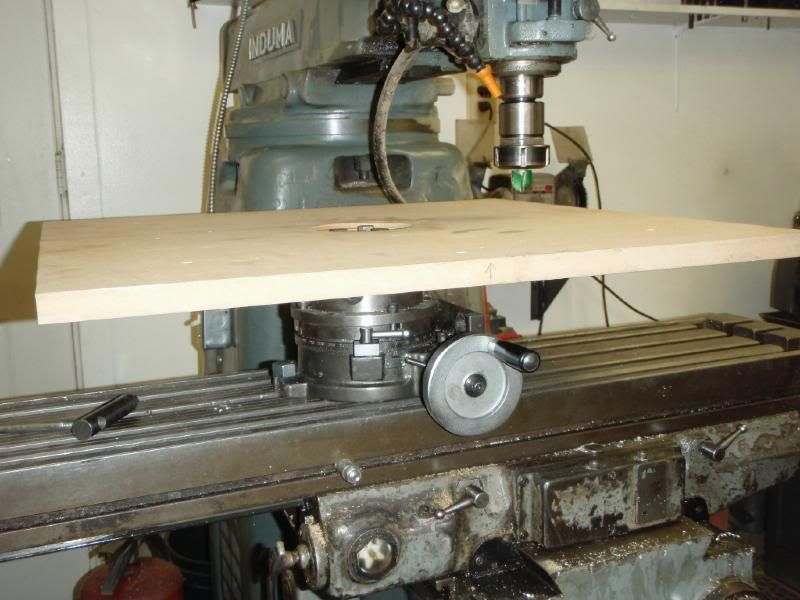
I set the bit 7-1/2 inches from the center of the rotary table and that gives me 16 inches to the outside diameter on the wheel
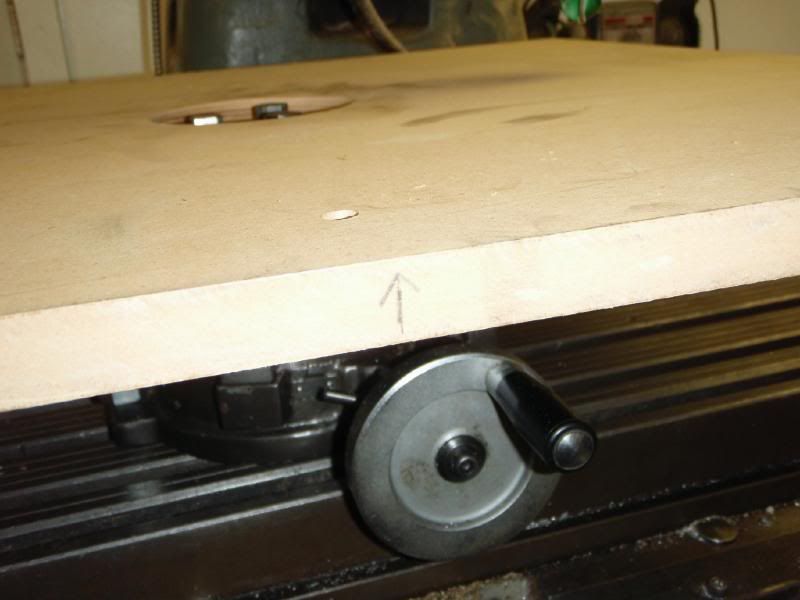
I set the depth at 1/2 inch and started turning the table
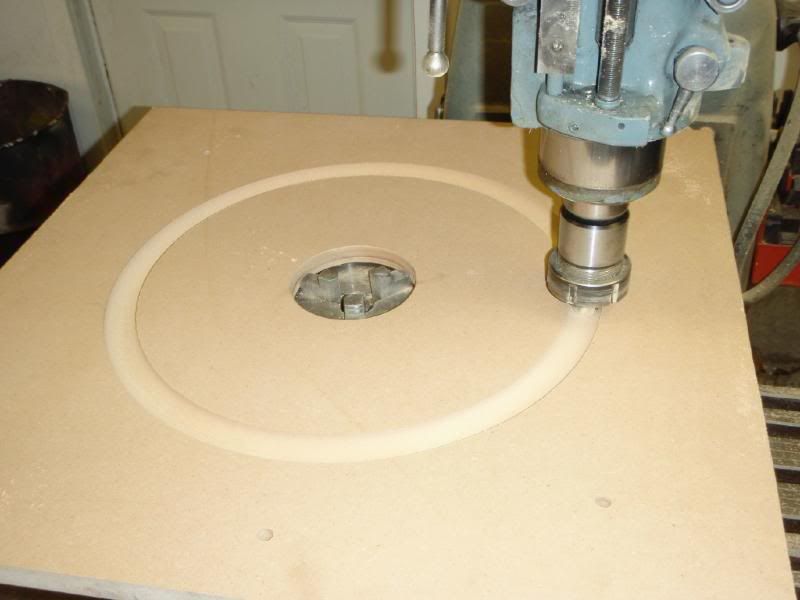